In an era of high-tech gadgets and automated tools, stick welding (officially known as Shielded Metal Arc Welding or SMAW) often gets dismissed as outdated. With flashier alternatives like MIG and TIG dominating YouTube tutorials, you might wonder if this century-old technique still has a place in modern DIY garages. Let’s dig into why stick welding isn’t just surviving. It’s thriving among resourceful hobbyists, and how you can master it for projects ranging from garden sculptures to emergency repairs.
What Makes Stick Welding Unique (And Why It’s Not Going Away)
Stick welding uses a consumable electrode coated in flux to create an electric arc between the rod and the workpiece. The flux melts, forming a gas shield that protects the weld pool from contaminants like oxygen and nitrogen. Here’s why it remains a staple:
- Brutal Simplicity
- No gas cylinders, wire feeders, or complex settings. Just a power source, electrode, and ground clamp.
- Works with basic 240V outlets or portable generators. Ideal for remote repairs on farm equipment or outdoor sculptures.
- Dirt Tolerance
- Unlike gas-shielded methods, stick welding tolerates surface impurities. A quick grind or wire brush prep often suffices.
- Perfect for restoring vintage tools, farm equipment, or outdoor structures exposed to weather.
- Cost Efficiency
- Entry-level stick welders cost a fraction of MIG/TIG setups. Electrodes are affordable and store indefinitely in dry conditions.
- Material Versatility
- Weld steel, cast iron, stainless steel, and even some nickel alloys with the right electrode.
Stick vs. MIG vs. TIG: Which Wins for DIY Projects?
Factor | Stick Welding | MIG Welding | TIG Welding |
---|---|---|---|
Learning Curve | Moderate (arc control) | Low (easy to start) | High (coordination) |
Portability | High (no gas) | Low (gas tanks) | Moderate (small tanks) |
Material Thickness | 1.5 mm to 12+ mm | 0.8 mm to 10 mm | 0.5 mm to 6 mm |
Outdoor Use | Excellent | Poor | Poor |
When Stick Shines:
- Fixing cracked tractor buckets in a dusty barn.
- Building heavy-duty trailer frames.
- Repairing cast-iron vintage tools.
Electrode Selection: Decoding the Numbers
Electrodes like 6013, 7018, and 6011 aren’t random digits. They’re codes that tell you exactly how they perform:
- First Two Digits: Tensile strength (e.g., 60 = 60,000 psi, 70 = 70,000 psi).
- Third Digit: Welding position (1 = all positions, 2 = flat/horizontal).
- Fourth Digit: Flux type and current (AC vs. DC).
Top Electrodes for DIYers:
- 6013: Smooth arcs, minimal splatter. Great for sheet metal and thin stock.
- 7018: Low-hydrogen rods for strong, crack-resistant welds on structural steel. Store in a heated rod oven to prevent moisture absorption.
- 6011: Deep penetration for rusty or dirty metal. Runs on AC or DC.
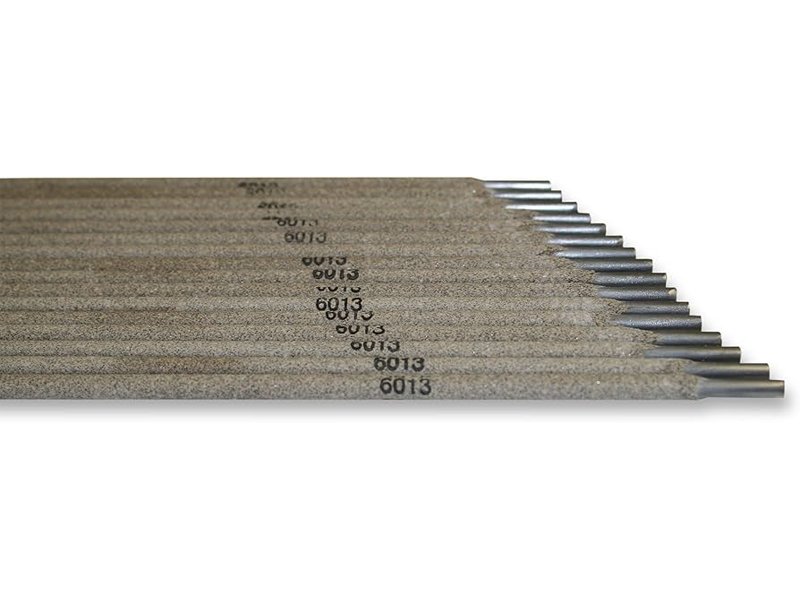
Mastering the Arc: Pro Techniques for Clean Welds
Strike and Maintain:
- Scratch Start: Gently scratch the electrode tip against the metal like a match.
- Drag Angle: Hold the rod at 15–20 degrees in the direction of travel.
- Arc Length: Keep it tight (1–3mm). A long arc causes sputtering and porosity.
Reading the Puddle:
- A well-controlled puddle looks like a shiny, fluid oval. If it’s wide and flat, reduce amperage. If it’s narrow and high, increase amperage.
Amperage Cheat Sheet:
- 1.5mm Steel: 50–70A (use 1/16” or 2.5mm electrodes).
- 3mm Steel: 80–110A (3/32” or 2.4mm electrodes).
- 6mm Steel: 120–160A (1/8” or 3.2mm electrodes).
Common DIY Mistakes (And How to Fix Them)
- Sticking Electrodes
- Cause: Low amperage or hesitant arc strikes.
- Fix: Crank up amps by 5–10% and practice quick, confident strikes.
- Porosity (Bubbles in the Weld)
- Cause: Moisture in electrodes or drafts disrupting the gas shield.
- Fix: Bake damp rods at 120°C for 1 hour. Shield your workspace with a tarp.
- Slag Inclusions
- Cause: Improper slag removal between passes.
- Fix: Chip slag with a chipping hammer, then wire-brush before the next pass.
Case Study: Building a Fire Pit in 6 Hours
A DIYer used stick welding to construct a steel fire pit from scrap materials:
- Design: Cut 12 trapezoidal panels from 3mm steel plate using an angle grinder.
- Welding:
- Tack Welds: 6011 rods at 90A to handle mill scale.
- Final Passes: 7018 rods at 110A for clean, strong seams.
- Finishing: Hit welds with a flap disc, then apply high-temperature paint.
Total Cost: 40 (electrodes and consumables) vs. 40 (electrodes and consumables) vs. 300+ for a pre-made fire pit.
Safety: What Most Tutorials Don’t Tell You
- Fume Risks: Even outdoors, wear an N95 mask. Manganese in fumes can cause neurological damage with prolonged exposure.
- UV Exposure: A single arc flash can sunburn your eyes. Use a #10 shade lens minimum.
- Fire Prep: Keep a CO2 fire extinguisher nearby. Sparks can travel 10 meters and ignite dry leaves.
The Future of Stick Welding: Smarter Tools, Same Soul
- Inverter Technology: Newer stick welders weigh under 5kg, fit in a backpack, and offer precise DC output for smoother arcs.
- Eco-Friendly Fluxes: Biodegradable flux coatings are in development, reducing landfill waste from used rods.
- AR Training Apps: Apps like WeldSim use augmented reality to help beginners practice rod angles without wasting materials.
Final Verdict: Who Should Stick With Stick?
Stick welding isn’t for everyone, but it’s indispensable for:
- Budget-Conscious DIYers: No ongoing gas costs.
- Rural or Off-Grid Users: Works with generators and minimal infrastructure.
- Vintage Restoration Fans: Repairs cast iron stoves or antique car frames authentically.
If you value simplicity over speed and durability over dazzle, stick welding is far from obsolete.